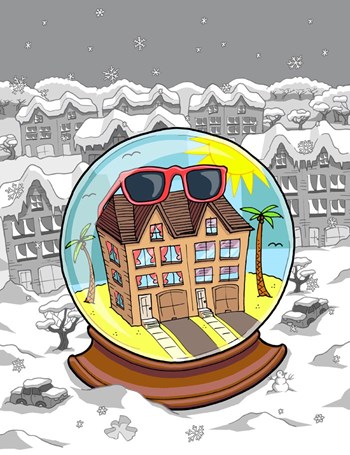
Good property managers need to be one step ahead of the game, and September is no time to be caught flat-footed. The once-packed swimming pool is now virtually empty, and the kids who filled it weeks ago are now lugging school backpacks around. The temperature is starting to dip at night, and there’s no time to waste—winter is coming and it’s time to get buildings and amenities ready for colder weather. Preparing for winter involves a number of tasks for the property manager, starting with draining the pool and ending with test-firing the boiler before the first frost.
Pool Prep
The first step in getting the pool ready for winter is to draw the water level down 10 to 18 inches, just below the skimmers, according to Glenn DiLoreto, president of Clear Blue Pool Management in Hackettstown. Once the water is lowered, winterizing chemicals are added “to keep the water as clear and algae-free as possible over the winter,” says DiLoreto. The next step is using a blower to clear out all the pool lines and adding anti-freeze to the lines for added precaution against freezing, he says.
Turning his attention to the pool area, DiLoreto recommends power-washing all the pool furniture before putting it in storage. In addition to water, he frequently adds a degreaser to the power wash mix to rid the furniture of accumulated suntan lotion. Also put away the pool’s vacuuming equipment for the winter, along with any handrails and ladders, which need to be unbolted before storing, he says.
While the pool equipment is being tucked away, DiLoreto says it’s a good time to take a full inventory, to generate a list of missing or damaged equipment.
Finally, says DiLoreto, the safety cover should be applied over the pool, both for aesthetic and insurance reasons. If the cover is installed correctly—anchored into the pool and drawn very tight—it should support the weight of a person, he says. With the cover on, DiLoreto says it’s time to make sure all of the pool’s entry gates are locked and all keys delivered back to the management office.
On the pool personnel front, DiLoreto asks his current lifeguards if they are open to coming back the following spring and compiles a list of possible returnees. “I contact them over the winter, usually during winter break, when they’re home from college. Or if they’re in high school, over that winter break. I know that they’ll be home,” says DiLoreto. “Usually by that time, they’ll have a good idea if they’re going to be back next season. That’s the key—do as much staffing and recruiting as you can over the winter.”
Planning for next spring’s opening can also be done over the winter, says DiLoreto. Using the inventory of missing equipment that was generated during the pool closing, he advises that you purchase those items over the winter. “In spring, it gets too crazy with everything having to happen before Memorial Day. You want to try to get as much as possible out of the way beforehand,” he says.
Communities that plan on keeping their pool water next year—versus pumping all the water out and acid- washing the pool surfaces—will also need to regularly treat their water over the winter, says DiLoreto. “Over the fall and right after the freeze, you want to apply chlorine and algaecide at least once a month so that the pool water stays relatively clean,” he says. “Otherwise when you take the cover off in the spring, it’s going to be green and black and you’ll have to spend a lot of time, energy and purchase chemicals to turn it around again.”
Don’t Forget the Clubhouse
Although every HOA will get its pool ready for winter, “The biggest thing we run into is communities that fail to winterize their clubhouse or pool bathrooms and showers,” says James Rademacher, CEO of Rezkom Enterprises in Ocean Township.
If not properly winterized, the clubhouse’s pipes can freeze and burst, making a huge mess and necessitating an expensive cleanup, says Rademacher, whose firm performs a variety of maintenance services for HOAs.
According to Rademacher, clubhouses that aren’t used year-round, or ones that shut off their heat, need to have all water lines, sinks, toilets, and showers drained and blown out. After blowing out all pipes, anti-freeze is put in toilet bowls and sinks to keep them from cracking. He says that sink drains (“J” bends) should be filled with antifreeze, or taken out entirely.
Moving outside the clubhouse, Rademacher says HOAs with tennis courts need to pull their nets down and store them in a dry space over the winter. Basketball nets can also be taken down, although Rademacher says it may actually be cheaper to simply replace them every other year or so than paying staff to install and uninstall them yearly.
Gutters are another area that definitely need preparation for winter. Backed-up gutters can lead to water collection and the formation of ice dams—which can be extremely serious for any condominium. Ice dams result when poor insulation or other factors cause roof snow to melt and slide down the roof, re-freezing as it reaches the cooler surface area closer to the eaves, or hits a plugged-up gutter. More and more water accumulates behind this layer—or “dam”—or ice, and the pooled water will eventually damage shingles and other roofing structures, leading to leaks, damage, and potentially very expensive repairs.
Rademacher says he prefers cleaning gutters by hand to using blowers because the latter technique tends to “make a mess” over the side of a building. After cleaning downspouts, he has his crews drop an object through to see if they are clogged. If they find an impediment, he has his crews take the downspouts apart and clean them by hand. For HOAs whose gutters empty into a sub-surface (underground) drainage system, Rademacher recommends blowing the system out to clear it of debris.
Furnaces Need Cleaning
For most co-ops or HOA’s with central boilers (generally found in converted apartments or mid- to high-rise buildings), September is the time to start getting them ready for winter, says Andrew Talkow, president of Manhattan Welding Company in Hillside, which performs boiler and burner maintenance and replacement. Getting the boiler ready starts with a thorough cleaning of its two compartments—one that holds the water, and the other in which combustion takes place. When cleaning, Talkow says that particular attention should be given to the oil filter and strainer, the low-water cutoff valve and the firing mechanism.
Once the boiler is cleaned, its firing mechanism should be tested with an “electronic combustion efficiency analyzer,” says Talkow. The analyzer checks the ratio of fuel to air, along with the temperature of the smokestack—all of which dramatically affect efficiency. Based on the results of the analysis, the boiler can then be tuned up for maximum money savings, and also to reduce soot and smoke, “which collects inside the boiler and actually renders it less efficient and eventually causes other problems,” Talkow says.
Chimneys and flues should also be checked for blockages and air drafts, says Talkow. Furnace contractors generally only check and clean the bottom portion of the chimney through a trap door at the base. In contrast, the upper chimney is generally checked by a chimney technician or “sweep,” who can be called in seasonally to give the entire chimney structure a much more thorough cleaning.
Before the weather starts getting colder, Talkow recommends test firing the boiler. He also notes that an annual inspection and test firing may even be mandated by an association’s insurance company before the insurer will issue or renew a boiler insurance policy.
Test firing is best done by those who are familiar with the boiler unit and qualified to interpret what they observe, says Talkow. “You’re looking and listening. You’re using your five senses. Do you smell anything such as a fuel like gas? Do you see anything, a water leak? Do you feel heat coming out of areas where it shouldn’t? Do you hear a pump or a motor making a funny sound?” says Talkow. “These are the common clues that there is a problem; then they should call a specialist.”
Problems can also happen outside the furnace room itself, Talkow continues. He recommends a thorough inspection of pipes and heating fixtures throughout the building, with particular attention paid to water leaks, which absolutely must be remedied before winter really kicks in. “Every time you have a leak, you end up adding fresh water to the boiler to make up for the leak,” he says. “And with fresh water comes fresh minerals and air—the two items that really attack the boiler and shorten its useful life span.”
For this reason, Talkow says it’s important to talk with owners and scrutinize the whole system for leaks. “Very often, you’ll find a radiator valve in some apartment that keeps dripping and the person doesn’t care, or they think its minor and not a big deal. But it has devastating consequences in the long run.” Talkow says that owners need to be advised that instead of just putting a pan on the floor by the radiator and periodically emptying it, they need to notify management.
If a furnace has been cleaned and tuned up and still suffers from high fuel consumption, Talkow says it may be time to consider replacement. “If the boiler is of a certain age, [a board may] want to consider something more fuel efficient.” Inefficient boilers as young as six years old may be good candidates for replacement due to rapidly changing technology, he says. “Over the past five years, we’ve seen a dramatic increase in high-efficiency equipment,” he says.
Another option for older, inefficient boilers is retrofitting them with “energy management controls,” which control the boiler based on outdoor temperatures, says Talkow. “It actually can be set to run different temperatures at different times of the day in proportion to the outside temperature, so if the outside temperature gets colder it will run the boiler to provide more heat.”
And the benefits of energy management controls extend beyond money savings, he says. “We believe they’re a tremendous fuel saver for most buildings, and they extend the life of the boiler because they can get the boiler to operate on a more even schedule as opposed to running 100 percent and turning off.”
With the boiler system running at full efficiency and the rest of the winterization checklist done, the property manager can finally relax. His or her work is done—at least until the first snowstorm.
Jim Douglass is the managing editor of New England Condominium magazine, a Yale Robbins, Inc. publication.
Leave a Comment