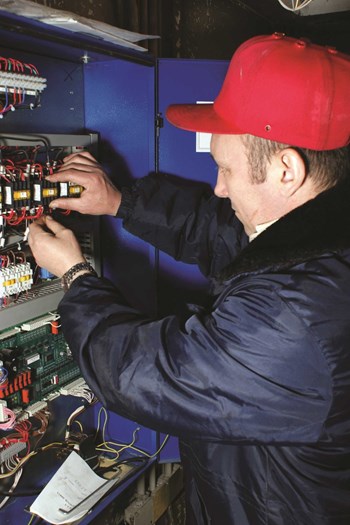
Like the automobile, the residential elevator is a mechanical marvel—and a fairly recent invention. If you’re a board member, a manager or just a unit owner of an urban or suburban co-op or condo development, chances are you probably use an elevator every day. We’ve all seen those elevator inspection reports but chances are that we don’t think about the inner workings of elevators very much. And it seems like the only times that elevators make the news is when something goes wrong, like the time a Chinese-food deliveryman was stuck for three days inside an elevator in a Bronx high-rise.
There have been elevator-like hoist devices throughout history, but in 1853, American inventor Elisha Otis invented a freight elevator equipped with a safety device to prevent the elevator from falling in case a cable broke. This led to widespread use of the equipment in the commercial and residential sectors of society.
How They Work
Today, there are basically two types of elevators in use—hydraulic and “rope-driven.” If you’re visualizing a rope similar to the one you used to climb in gym class, however, you’re way behind the times—today’s rope driven elevators contain six to eight lengths of wire or steel cable. These cables are attached to the top of the elevator cab and wound around a drive sheave in special grooves. The other ends of the cables are attached to a collection of metal weights equal to the weight of the car and a little less than half of its rated load. The counterweight slides up and down the shaftway on its own guide rails.
Chains or cables loop through the bottom of the counterweight to the underside of the car to help maintain balance by offsetting the weight of the suspension ropes. Guide rails that run the length of the shaft keep the car and counterweight from swaying or twisting during travel. Rollers are attached to the car and the counterweight to provide a smooth ride along the guide rails. An electric motor then turns the sheave. These motors are able to control speed, and allow for the elevator's smooth acceleration and deceleration. Signal switches also stop the cab at each floor level.
In a hydraulic elevator, the car is lifted by a hydraulic-fluid driven piston mounted inside a cylinder. The cylinder—containing oil or a similar substance—is connected to a pumping system. The pump forces fluid into the tank leading to the cylinder; when enough fluid is collected, the piston is pushed upward, lifting the elevator car on its journey. When the car is signaled that it is approaching the correct floor, the control system triggers the electric motor to gradually shut off the pump. To get the elevator to descend, the control system sends a signal to the valve operated electronically by a switch. When the valve is opened, the fluid flows out into a central reservoir, and the weight of the car and its cargo pushes down on the piston, driving more fluid out and causing the cab to move down.
Joe Rapine, business manager for the Philadelphia-based Local 5, International Union of Elevator Constructors, which covers 13 counties in New Jersey, says many people are “trying to get away from hydraulics” because of the contamination factor, in which oil can leak into the ground. Now, he says, to correct that problem, many manufacturers have ‘hole-less hydraulics” which eliminate the need for a well-hole or buried piping.
Still, says Brian Black, codes and safety consultant for National Elevator Industry Inc., hydraulics are very common on a nationwide basis. It’s rare that they’re used in tall buildings, but, “the majority of elevators in this country are two to three stories.”
There have been constant improvements in elevator design, but the most significant change, says Black, has been the development of solid-state controls. Software can be updated and modified on an as-needed basis. “It also allows remote monitoring by the elevator manufacturers—if there were an elevator exhibiting some problems in Trenton, the manager could call Otis in Farmington, and they often can do a stop-check right there,” he says.
Another change, says TinaMarie Cortina, spokeswoman for Liberty Elevator Corp. in Paterson, is that in traction elevators, rope grippers are now mandated by code. If an elevator should move on its own (because of an error), the rope gripper will sense this and grip the cable, preventing it from moving further.
Keeping Them Safe
Regardless of these changes, says Black, older elevators can work as long as they are maintained properly. “I’ve seen 100-year-old elevators that are operating very well,” he says. Still, owners might wish to change the interior or put in new lighting, new controls, better ventilation or other changes.
In New Jersey, the Department of Consumer Affairs (DCA) Elevator Safety Unit is the state agency that governs the Elevator Subcode and registers all elevator devices in the state, according to Lisa Ryan, DCA public information officer. This unit enforces the subcode and inspects elevators in state buildings and municipalities under the jurisdiction of the DCA’s Office of Local Code Enforcement. Municipalities give jurisdiction to enforce the Elevator Subcode to the DCA’s Elevator Safety Unit.
However, some municipalities have their own elevator subcode officials or use an outside contractor to enforce it. It’s called a “subcode” because it’s part of the state’s Uniform Construction Code (UCC).
What is exactly in the code? Like most building codes, it’s complicated, but Ryan gives some answers. Many of the administrative requirements, she says, haven’t changed since the Elevator Subcode was first drafted. Some are pretty basic: a permit is required to install a new elevator as well as to perform work (rather than ordinary maintenance) on an existing elevator; newly installed elevators must be registered with the state; existing elevators are subject to cyclical maintenance inspection and tests must be performed by inspectors licensed by the state.
“Some of the technical requirements of the codes in effect today are different from those of the prior codes,” Ryan adds. “However, because the Elevator Subcode is not a retrofit code, the technical requirements are only applicable to those codes that were in effect at the time [the elevator was installed or applied for].”
Most state codes, adds Black, are based on the American Society of Mechanical Engineers (ASME) Code A17.1. The panel that develops it contains both representatives of elevator manufacturers and top elevator inspectors.
Elevators in New Jersey must undergo basic annual inspections/tests once a year, with more complicated tests once every five years (once every three years for hydraulics). But many professionals say a more frequent maintenance/inspection schedule is ideal. Liberty, for example, has a variety of types of contracts that are custom-made for individual customers, says Cortina. Rapine advises users to seek a contract by which the elevator professional would spend an hour a month on each car.
What happens during a test? Hydraulic and traction tests are different, Cortina says. “Hydraulic elevators receive a `no-load’ pressure test on an annual basis that is conducted with the inspector and elevator company. The semi-annual hydraulic inspection is just done by the inspector and is less involved than the annual tests. For traction cars, the five-year full test is conducted with the inspector and the elevator tests. The annual test is done with the inspector and elevator company, and the semi-annual is done solely by the inspector.”
Tests, adds Black, include “basic things” such as whether the light in the car, the buttons and the ventilation system all work. “One of the more critical things,” he emphasizes, “is the door system—to make sure the car is leveling correctly so you don’t create a tripping hazard. This can be a challenge in both hydraulic or traction elevators. An empty elevator will level one way, but with 20 people it will be different.”
Whether the car closes correctly is critical as well, he says, but that can often be modified on site. “If it’s closing too quickly or too strongly, it can be adjusted.”
Of course, safety devices must also be tested. Brakes, buffers, stopping devices, emergency stopping devices, the elevator’s emergency fire service, are all important.
If the inspection reveals a problem, the inspecting agency gives a report to the owner or manager, who in turn must give it to his elevator contractor. The owner needs to correct the violations within a given time, and must re-check the device afterward. Often, says Black, modifications can be made while the elevator is still in operation—“it will only be out for a half-hour or so.” But if there’s a serious problem, Rapine says, “the inspector should `red-tag it” and shut it off.
What about costs? In New Jersey, they’re not hard to find out—they’re right in the Elevator Subcode, Section 12.6. Fees vary depending on the type of structure, who the enforcing agency is and other factors, but in general, tests and inspection fees are less expensive for hydraulic elevators, more expensive for “traction and winding drum elevators” up to 10 floors, and yet more expensive for traction elevators over 10 floors, with added fees for oil burners, counterweight governors and safeties, and auxiliary power generators. The schedules are somewhat complicated, and we recommend that managers and board members consult with their elevator contractors for a complete explanation.
Elevator Ailments
What are some of the most common problems affecting New Jersey residential elevators? Professionals interviewed for this article mentioned malfunctioning door locks and elevators that don’t level properly (i.e., stop an inch or more above or below the bottom of the outer door), among other things.
The main underlying problem with elevators, says Rapine, is a lack of maintenance. “The effect is that if you don’t have regular maintenance, you will have more problems, more shutdowns. This happens if you don’t take care of anything—even your car.”
Finally, it’s important to note that elevator contractors and inspectors are highly skilled, highly trained people. The unions typically have four-year apprenticeship programs, whether it’s Rapine’s Local 5; the New York-based Local 1 of the same union, representing employees of firms closer to New York (Liberty’s technicians are members of Local 1, although Liberty is also Local 5-certified so it can do work in southern New Jersey); or, in New York City, Local 3 of the International Brotherhood of Electrical Workers. The elevator manufacturers also do their own training. To become an inspector, applicants must have experience in elevator work, take additional seminars, be tested and then be licensed by DCA.
There are many sources to check out licensed elevator contractors: co-op and condo organizations; review sites; the union locals, and, of course, the pages and directories of The New Jersey Cooperator.
If your association’s buildings are elevator-equipped, it’s vital for both your livelihood and value that the devices are kept in top-notch operating condition. With good everyday upkeep, regular professional maintenance visits, and prompt attention to any abnormalities, your building’s elevator units will be on the up-and-up for decades to come.
Raanan Geberer is a freelance writer and a frequent contributor to The New Jersey Cooperator.
Comments
Leave a Comment