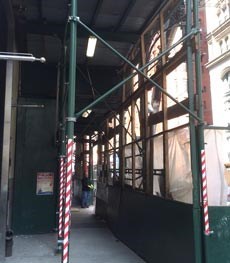
Walk down any street in any of New Jersey’s major cities and you may have to step around or go under one of the ubiquitous steel-and-plywood structures that shade urban sidewalks, more often than not festooned with wheat-pasted posters for everything from the hottest nightclub parties to new movies opening this weekend.
They’re called sidewalk sheds and scaffolds and these blue or green plywood platforms boosted up above street level by crisscrossing metal poles and girders are usually installed on buildings in the midst of an exterior repair program.
What's That Thing?
“Sheds are regularly used to protect workers (and the public, depending on the circumstances) from falling material, equipment, tools, construction debris etc.,” says Michael D'Aquino, a spokesman for the United States Department of Labor’s Occupational Safety and Health Administration (OSHA).
By contrast, a scaffold is a temporary work platform, either suspended from the roof or some other part of a building or built up from the ground, typically with a system of pipe sections. Both types of structures are often in place for years at a time, and can become tremendous eyesores, with flapping plastic and cracked, peeling paint that erode even the most luxurious building's curb appeal.
“Pieces of scaffolding include, but are not limited to, base plates, mudsills, screw jacks, planking, cross-bracing, uprights, guardrails, toe boards, tie backs, outriggers, means of access (ladders), and side frames,” D'Aquino explains.
There are several types of scaffolds available for use, each dependent on the project being done, according to Alan Kline, the owner of Boston-based Lynn Ladder & Scaffolding Co. Inc. and a board member of the Scaffold Access and Industry Association (SAIA). “You've got scaffolding just for contractors that do framing and build houses, then you've got steel scaffolding which is frames and braces. Then you've got suspended scaffolding which you wouldn't use on a new building. Then you have mass climbers, which are always used on bigger buildings. You've got a lot of different stuff you can use.”
New Jersey's Division of Codes and Standards, which is part of the Department of Community Affairs (DCA), regulates construction laws and building codes with The New Jersey State Uniform Construction Code (UCC) Act. While New Jersey local government is free to create rules and regulations regarding scaffold and sidewalk shed usage and safety, OSHA sets federal job site safety and health standards that all U.S. states must follow which supersede any local laws.
Safety First
So, why do we need them? These structures are designed to prevent injuries and save lives.
In May of 2008, two construction workers suffered fatal falls and one was injured when their scaffold collapsed at a Bayonne-based construction site.
According to OSHA, “An estimated 2.3 million construction workers, or 65 percent of the construction industry, work on scaffolds frequently. Protecting these workers from scaffold-related accidents would prevent 4,500 injuries and 50 deaths every year, at a savings for American employers of $90 million in workdays not lost.” In fact, citations for scaffold construction and general requirements violations were the third most issued by OSHA in 2013.
Construction work that necessitates the use of scaffolding is inherently more dangerous than another job that doesn’t require one to be elevated at great heights, but is there a type of scaffold that is safer than others? Kline says no, and maintains that scaffold safety is mostly dependent on those using the equipment.
“The way OSHA reads is on every single job for the entire shift, you must have a competently trained person who can identify the hazards of the job and has the authority to correct them,” Kline says. “If it's a job over 25 feet in the air, it has to be designed by a professional engineer. And you would still need someone on the job site to watch what's going on. A typical scaffolding accident would be somebody falling off the plank because it didn't have the guard rails on it, which goes back to the competent person being responsible,” Kline says. “That's why we don't lose cases. We give them the equipment and whether they choose to use it or not, it's the competent person's responsibilities. There are a lot of issues too with kids under the age of 25 that do construction work that are alcoholics, drug addicts, just plain stupid punks,” Kline says.
The pros say they believe continuing education is the key to scaffold safety. Dominick Frontera, the president of Ridgefield Park-based World Wide Construction Restoration Waterproofing & Roofing Inc., requires all construction workers take safety courses from Bayonne-based Total Safety Consulting and hold the required license(s) to perform scaffolding jobs.
As an SAIA board member, Kline also regularly participates in scaffold safety courses and seminars the national organization provides. According to SAIA's website, the organization works to “be the unified voice of the scaffold and access industry; promote safety by developing educational and informational material; conducting educational seminars and training courses; provide audio-visual programs and codes of sage practices and other training and safety aids; work with state, federal and other agencies in developing more effective safety standards; reduce accidents, thereby reducing insurance cost; and assist our members to become more efficient and profitable in their businesses.”
Insurance Issues
A permit is required to erect a scaffold in New Jersey. While specifics might differ between townships, cities and municipalities, generally, the city in which the scaffold will be erected will require proof of a license and insurance before a permit is issued. For example, Newark's Department of Engineering Division of Traffic and Signals requires the city of Newark to be named as additionally insured on the applicant's insurance policy. The city also demands that the insurer “indemnify and hold harmless the city of Newark, its agents, servants and administrators from and against all claims or actions at law, whether personal injury, property damage or liability.”
Newark also requires a separate hold harmless document ensuring Newark will not be held liable, a letter stating that competent individuals will install the scaffold according to OSHA standards and specifications, and lastly, proof of insurance coverage totaling at least $1 million.
In Newark, scaffolding permits are effective for 30 days from the date of issuance and if work is not completed within that time, the owner and contractor can agree to either renew it or they are
Prior to obtaining a scaffolding permit, a contractor must obtain comprehensive General Liability insurance in an amount equal to or exceeding $1 million, naming the city in which work is being done, its officers, employees and agents as an additional insured.
Who is Liable?
The construction professionals say that with respect to scaffolds and other equipment used by construction crews, condominium owners and associations are generally insulated from any resulting liability or payout when a worker or bystander is injured in an accident in New Jersey.
“Legal consequences with respect to the OSHA Act will depend on the responsibilities of an employer at a worksite,” D'Aquino says. “Based on the facts gathered during an OSHA investigation, a company who is identified under at least one of the criteria under OSHA’s multi-employer worksite policy (as an exposing, creating, controlling, and/or correcting employer) can be subjected to actions under the OSH Act.”
Frontera says that if one of his workers is injured on the job, his company’s insurance will cover medical expenses. While Frontera notes his company uses their own scaffolding equipment, he says that if an injury were to be caused by defective scaffolding rented from an outside source, a report would be filed and submitted for review to the scaffold safety company that overlooks the rented scaffold equipment.
While such contractual provisions are relatively standard in the industry, it is always a good idea for all homeowners and condo boards to look for such language in a contract before work even begins. As a form of best practice, Richard Resnick, an agent at Schechner Lifson Corp. in Chester, urges associations to create a contract with a general contractor prior to the commencement of a project to further ensure protection from vicarious liability via a hold harmless indemnification agreement. General liability insurance is also a must when it comes to protecting an association for liability.
“In the insurance clause, you're going to indicate and now you need General Liability insurance with a limit no less than $1 million. The GL policy for a contractor should have full contractual and should respond on an ongoing and completed operations basis. The condo association should be named as additional insured primary,” Resnick says.
In urban areas known for old buildings and large skyscrapers, there will likely not be a time when it is completely devoid of sidewalk sheds and scaffolding but one day, maybe the look will be more appealing. The important thing to remember is that they keep the people of the Garden State safe and sound.
Keith Loria is a freelance writer and a frequent contributor to The New Jersey Cooperator. Editorial Assistant Enjolie Esteve contributed to this article.
Leave a Comment