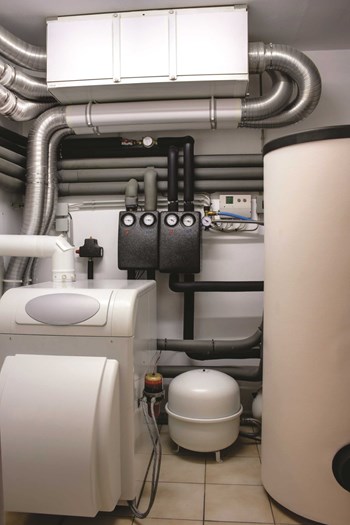
The rarely stated—but all too well understood—Murphy’s Law for Boilers—asserts that if your boiler quits working, it will do so on Christmas or New Year’s Eve, or at 4:45 p.m. on the coldest day of the year. With some planning, though, that broken-down boiler won’t be yours on those inopportune frigid days. An association’s management and staff can head off a worst-case scenario by scheduling regular maintenance and keeping an educated eye on the whole system.
With the heating season in the Garden State extends from October to May, being certain that your building’s boiler will function well should be a high-priority concern for each building’s management. Maintenance also saves money by improving efficiency and extending the useful life of mechanical equipment.
Maintenance Musts
Stephen Samouhos of Evco Mechanical Corp in West Orange tells us that, “In general, the boiler room ought to have a preventative maintenance visit by a qualified technician at least twice a year, once before the start of the heating season and once at the end.”
According to Mitch Leibowitz of Passaic's Pruzansky Plumbing, Heating, and Air Conditioning, “The first maintenance will be somewhere between Labor Day and Columbus Day. That would include filling the system, testing it, checking pressure, checking all the gauges, the electrics, and obviously firing it up and making sure there are no leaks and that everything's performing properly.”
“Around Memorial Day,” Leibowitz continues, “I shut everything down, drain everything properly. I wouldn't consider it a full maintenance, because we're still going to come back before the heating season, but definitely some things that can help with preventative issues for off season.”
Don't be tempted to skip the end-of-season maintenance. “Wear and tear accrued over the heating season can continue to degrade the equipment,” says Samouhos, “even while it is dormant. Combustion residues can be acidic and corrode metals.”
Ignoring that May maintenance can also lead to inconvenient or uncomfortable situations come wintertime. Leibowitz gives an example: “Sometimes boilers are not just supplying heat for the building—they're used as combination suppliers for hot water too. If you don't shut the heating part of it off correctly, that hot water could bypass, get into the heating system, and start providing heat when you're not calling for it. It's much better to make sure it's done right than getting heat in the building on an 85-degree weekend day.”
When Extra Upkeep is Needed
'Regular' servicing might mean different things for different boilers. More frequent maintenance and cleaning of a system depend largely on the needs of the particular system. Clevie Stewart, a licensed oil burner inspector and owner of Precision Combustion Consultants, Inc. in the Bronx, notes that a steel-construction boiler, installed correctly and maintained properly (including chemical water treatment service), can last 25 to 30 years. But if improperly installed, a new boiler can begin to leak in just two or three years after installation.
He advises property owners, contractors, architects and engineers and managers with older boilers that they have their systems inspected every few months.
Oil burners need more frequent cleaning than those run on natural gas. A major cleaning is an 8- to 10-hour process, and the boiler must be shut off and allowed to go cold first, which is why it makes sense to do a major cleaning before the heating season starts. In a supplementary cleaning, on the other hand, the boiler is cleaned while it’s still operating. This type of cleaning is roughly half the cost of a major cleaning. Experts recommend that No. 2 oil-burning boilers have supplementary cleanings at least two or three times during the heating season, in addition to the major cleaning. A building with a boiler that’s burning dirtier No. 6 oil should have an outside company come and clean the boiler monthly during the heating season.
Steel, as opposed to cast-iron, boilers need chemical treatments for the water they circulate. Chemical servicing should be done monthly during the heating season.
Samouhos explains that newer boilers make this easier. “Many of the modern boilers include control systems that can used for remote-telemetry and condition-based maintenance visits. In this case, data from the boilers themselves can be used to identify if an unscheduled maintenance visit would be useful in order to avoid a more costly potential breakdown or emergency in the future.”
Spotting Trouble
While much of the work needed for a boiler is done by outside companies, some things can—and should—be done by the building’s superintendent or another building-maintenance staff member tasked with the job. Leibowitz says, “The super should have some kind of working knowledge of how these boilers function and how to at least shut down and start them up in case of an emergency.”
Richard Jayson owner of The Jayson Company in Union adds, “The super should be taught about blow-down of the low water cut off.” And according to Samouhos, “A good service company ought to provide training and review with the super during each maintenance visit to refresh the super’s memory on equipment operation.”
Properly maintaining a boiler isn’t just checking the machine from time to time and responding to emergencies; it’s about being vigilant. “A building or HOA staff should always keep a watchful eye on the gauges,” says Leibowitz. “Monitor the daily intake of water into the system by checking the water meter. Check the stack temperature every day to see that the temperature is not elevated above normal.” According to the pros, a logbook should be used to record all readings. It makes deviation from normal easy to spot, and besides, it's required by law.
Jayson says the super should also “check for and report any leaks that are identified.” Indications of leaks might be condensation, wet spots on equipment or the floor (in the case of buried heating lines), or obvious dripping of water from the system. In addition, the super should monitor the fuel strainer, which can have residue build up that will reduce the system’s efficiency.
And just as your average motorist knows more or less how his or her car sounds when it’s running properly, a super should have an ear for the building’s heating system. “The super should know what the system sounds like when running properly. He should be able to differentiate unusual sounds that could be signs of problems,” Stewart says.
Obvious signs, however small, should never be ignored. A quick phone call to the service company could alert the super to the need to shut down the system to avoid catastrophe.
Legally Speaking
In New Jersey, says Leibowitz, “There's no law requiring maintenance to boilers, but the state does do yearly inspections for mid-rise and high-rise. They'll inspect and tell you if something needs to be updated or changed based on codes. But in terms of maintenance, no, there's no requirement that Harmon Cove Towers has to order maintenance on their boiler three times a year, per the state of New Jersey.”
The building's day-to-day boiler checks are regulated, though. “As per New Jersey Administrative Code 12:90,” says Samouhos, “the building super in most mid- and high-rise buildings actually needs to visit the boiler room every two hours to complete state-mandated inspections of operating conditions and enter his inspection results into the boiler-room logbook. This is a state requirement enforced by the Department of Labor and can result in significant fines if the logbook is inspected by the state and found not to be maintained. Such inspections are required even during the summertime when the boilers are presumably inactive.” Compliance means either a sleepless superintendent...or hiring three shifts of workers. Neither one sounds very appealing to boards, residents, or supers.
However, the Department of Labor Bureau of Boiler and Pressure Vessel Compliance has taken pity, and according to Samouhos, “provides a state program called Exception 6 whereby boilers that normally would require a site inspection every two hours will only need a site inspection twice per day, and only during the regular work hours of the week. Many owners are looking to this alternative for meeting state maintenance requirements in their buildings.”
Although conversion to cleaner-burning oils or natural gas hasn't been mandated in New Jersey as it has in New York, many boards have decided to switch to gas due to environmental concerns and lower cost. Currently, natural gas is cheaper to buy and also, because it's more efficient, less expensive to run. It requires fewer regular service visits as well. The two types of systems aren’t the same, though, and require different maintenance. Failure to notice warning signs of trouble, especially with a natural-gas system, could be disastrous, so re-education of all staff members who are ever responsible for the boiler is critical.
Another thing boards and managers should watch is being penny wise and pound foolish. For instance, when it comes to taking care of tubes leaking in a boiler, Stewart avoids the piecemeal approach. “We recommend that when you notice a few tube leaks, you replace them all,” he says. By the same token, calling on your professional maintenance service more often than strictly necessary can add to the life of your expensive-to-replace boiler.
And, says Leibowitz, “It's not just the cost of the boiler,” which is bad enough. “When you're dealing with these buildings, how do you get the boiler in? How do you get the boiler out? There's a lot of things that go into it. Sometimes you have to take the whole thing apart just to get it out. It's not always on a roof where you can just crane it up.”
A boiler should work well for decades. Just how long it lasts depends partially on its construction and how it was installed, but mostly on how it is maintained. Maintaining a boiler properly is of paramount importance not only because it creates a safer atmosphere for residents and building staff, it also saves money from not wasting energy in running a boiler inefficiently.
Jonathan Barnes is a freelance writer and regular contributor to The New Jersey Cooperator. Staff writer Judy Hill contributed to this article.
Leave a Comment